Equipment sizing: Difference between revisions
Rollman222 (talk | contribs) No edit summary |
Rollman222 (talk | contribs) No edit summary |
||
Line 18: | Line 18: | ||
Steps should be taken to account for potential failures of cooling/heating streams to prevent or minimize damage to equipment and injury to operators. | Steps should be taken to account for potential failures of cooling/heating streams to prevent or minimize damage to equipment and injury to operators. | ||
<ref>Sinnott, R. K., and Gavin P. Towler. Chemical Engineering Design / Ray Sinnott, Gavin Towler. 2013</ref> | |||
===Design Pressure=== | ===Design Pressure=== | ||
Line 28: | Line 29: | ||
The specified pressure is usually near the relief valve at the top of the vessel. | The specified pressure is usually near the relief valve at the top of the vessel. | ||
<ref>Sinnott, R. K., and Gavin P. Towler. Chemical Engineering Design / Ray Sinnott, Gavin Towler. 2013</ref> | |||
==Vessel Geometry== | ==Vessel Geometry== | ||
Line 34: | Line 36: | ||
Typically pressure vessels are cylinders with at least a 2:1 ratio of height to width. 3:1 and 4:1 ratios are most common. | Typically pressure vessels are cylinders with at least a 2:1 ratio of height to width. 3:1 and 4:1 ratios are most common. | ||
<ref>Sinnott, R. K., and Gavin P. Towler. Chemical Engineering Design / Ray Sinnott, Gavin Towler. 2013</ref> | |||
===Pressure Vessel Orientation=== | ===Pressure Vessel Orientation=== | ||
Pressure vessels can be oriented either vertically or horizontally. Vertical vessels are more common because they use less land space and the smaller cross-sectional area of the vessel allows for easier mixing. Horizontal vessels are used when more phase separation is required because larger cross-sectional areas allow for less vertical velocities and therefore less entrainment. Settling tanks and flash vessels are typically horizontal for this reason. Horizontal vessels also allow easier cleaning, so heat exchangers are primarily horizontal. | Pressure vessels can be oriented either vertically or horizontally. Vertical vessels are more common because they use less land space and the smaller cross-sectional area of the vessel allows for easier mixing. Horizontal vessels are used when more phase separation is required because larger cross-sectional areas allow for less vertical velocities and therefore less entrainment. Settling tanks and flash vessels are typically horizontal for this reason. Horizontal vessels also allow easier cleaning, so heat exchangers are primarily horizontal. | ||
<ref>Sinnott, R. K., and Gavin P. Towler. Chemical Engineering Design / Ray Sinnott, Gavin Towler. 2013</ref> | |||
===Head Design=== | ===Head Design=== | ||
[[File:pressure vessel heads.jpg|thumb|Seen above: (a) ellipsoidal, (b) torisphereical, and (c) hemispherical | [[File:pressure vessel heads.jpg|thumb|Seen above: (a) ellipsoidal, (b) torisphereical, and (c) hemispherical<ref>{{Pressure Vessel Heads. Inspection-for-Industry. http://www.inspection-for-industry.com/pressure-vessel-heads.html}}</ref>]] | ||
There are three different designs for the ends of the pressure vessel: hemispherical, ellipsoidal, and torispherical. Hemispherical heads are best for high pressure systems, they provide the largest internal volume of the three options, they are half the thickness of the shell, and are the most expensive to make and combine with the shell. Ellipsoidal heads are cheaper than hemispherical heads and provide less internal volume, they are the same thickness as the shell, and are most common for systems with greater than 15 bar. Torispherical heads are the cheapest of the three options, and are most commonly used when pressures do not exceed 15 bar. | There are three different designs for the ends of the pressure vessel: hemispherical, ellipsoidal, and torispherical. Hemispherical heads are best for high pressure systems, they provide the largest internal volume of the three options, they are half the thickness of the shell, and are the most expensive to make and combine with the shell. Ellipsoidal heads are cheaper than hemispherical heads and provide less internal volume, they are the same thickness as the shell, and are most common for systems with greater than 15 bar. Torispherical heads are the cheapest of the three options, and are most commonly used when pressures do not exceed 15 bar. | ||
<ref>Sinnott, R. K., and Gavin P. Towler. Chemical Engineering Design / Ray Sinnott, Gavin Towler. 2013</ref> | |||
==Stresses and Strains== | ==Stresses and Strains== | ||
There are a variety of potential stresses on a pressure vessel that must be accounted for during design and construction: | There are a variety of potential stresses on a pressure vessel that must be accounted for during design and construction: | ||
<ref>Sinnott, R. K., and Gavin P. Towler. Chemical Engineering Design / Ray Sinnott, Gavin Towler. 2013</ref> | |||
* Internal and external pressure | * Internal and external pressure | ||
Line 74: | Line 80: | ||
Typically walls are much thicker. In high pressure vessels, internal pressure has the largest magnitude. In low pressure vessels, wall thickness is designed to resist vacuum. | Typically walls are much thicker. In high pressure vessels, internal pressure has the largest magnitude. In low pressure vessels, wall thickness is designed to resist vacuum. | ||
<ref>Sinnott, R. K., and Gavin P. Towler. Chemical Engineering Design / Ray Sinnott, Gavin Towler. 2013</ref> | |||
===Head thickness=== | ===Head thickness=== | ||
Alternate equations govern the appropriate head thickness: | Alternate equations govern the appropriate head thickness: | ||
Hemispherical: | Hemispherical: | ||
Line 91: | Line 98: | ||
<math>Thickness = \frac {0.885PRc} {SE - 0.1P}</math> | <math>Thickness = \frac {0.885PRc} {SE - 0.1P}</math> | ||
R<sub>c</sub> is the crown radius. | R<sub>c</sub> is the crown radius. | ||
<ref>Sinnott, R. K., and Gavin P. Towler. Chemical Engineering Design / Ray Sinnott, Gavin Towler. 2013</ref> | |||
===Corrosion Allowance=== | ===Corrosion Allowance=== | ||
Line 98: | Line 106: | ||
In heat exchangers where wall thickness can affect heat transfer, smaller margins are used. | In heat exchangers where wall thickness can affect heat transfer, smaller margins are used. | ||
<ref>Sinnott, R. K., and Gavin P. Towler. Chemical Engineering Design / Ray Sinnott, Gavin Towler. 2013</ref> | |||
==Materials of Construction== | ==Materials of Construction== | ||
The materials used in pressure vessels must maintain their strength under design conditions, withstand variation due to changing process conditions, and must resist corrosion. Commonly used materials include carbon steel, stainless steel, and various nickel alloys. | The materials used in pressure vessels must maintain their strength under design conditions, withstand variation due to changing process conditions, and must resist corrosion. Commonly used materials include carbon steel, stainless steel, and various nickel alloys. | ||
<ref>Sinnott, R. K., and Gavin P. Towler. Chemical Engineering Design / Ray Sinnott, Gavin Towler. 2013</ref> | |||
References: {{reflist}} | References: {{reflist}} | ||
<br> | <br> |
Revision as of 15:57, 7 February 2015
Author: Matt Nathal [2015]
Stewards: Jian Gong and Fengqi You
Vessel Specifications
The process requirements usually dictate specifications and parameters that the pressure vessel must fulfill. Some such requirements are:
- Min and Max design temperature
- Min and Max design pressure
Design Temperature
Maximum design temperature – highest mean metal temperature expected in operation plus a margin (typically 50°F).
Minimum design temperature – lowest mean metal temperature expected in operation minus a margin (typically 25°F).
Steps should be taken to account for potential failures of cooling/heating streams to prevent or minimize damage to equipment and injury to operators. [1]
Design Pressure
Normal operating pressure – the expected pressure of the process.
Maximum operating pressure – the highest expected pressure, potentially during startup, shutdown, or emergencies.
Design pressure – the maximum operating pressure plus a margin. The margin is typically the greater of: 10% of max operating pressure or 25 psi.
The specified pressure is usually near the relief valve at the top of the vessel. [2]
Vessel Geometry
Pressure Vessel Size and Shape
Typically pressure vessels are cylinders with at least a 2:1 ratio of height to width. 3:1 and 4:1 ratios are most common. [3]
Pressure Vessel Orientation
Pressure vessels can be oriented either vertically or horizontally. Vertical vessels are more common because they use less land space and the smaller cross-sectional area of the vessel allows for easier mixing. Horizontal vessels are used when more phase separation is required because larger cross-sectional areas allow for less vertical velocities and therefore less entrainment. Settling tanks and flash vessels are typically horizontal for this reason. Horizontal vessels also allow easier cleaning, so heat exchangers are primarily horizontal. [4]
Head Design
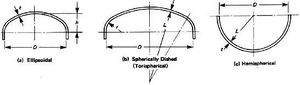
There are three different designs for the ends of the pressure vessel: hemispherical, ellipsoidal, and torispherical. Hemispherical heads are best for high pressure systems, they provide the largest internal volume of the three options, they are half the thickness of the shell, and are the most expensive to make and combine with the shell. Ellipsoidal heads are cheaper than hemispherical heads and provide less internal volume, they are the same thickness as the shell, and are most common for systems with greater than 15 bar. Torispherical heads are the cheapest of the three options, and are most commonly used when pressures do not exceed 15 bar. [6]
Stresses and Strains
There are a variety of potential stresses on a pressure vessel that must be accounted for during design and construction: [7]
- Internal and external pressure
- Weight of vessel
- Weight of contents
- Weight of internals (distillation trays, heating/cooling coils, packing supports)
- Weight of attached equipment
- Thermal expansion
- Cyclic loads caused by condition changes
- Friction loads
- Environmental loads (wind/snow/seismic)
Wall Thickness
There are two main stresses that can occur on the shell portion of the pressure vessel; hoop stress and longitudinal stress.
Hoop Stress:
Longitudinal Stress:
Where P is the pressure, D is the diameter, S is the max allowable stress, and E is the welded joint efficiency. The thicker of the two is chosen as the wall thickness. The minimum wall thickness (without considering corrosion allowances) is 1/16 inches.
Typically walls are much thicker. In high pressure vessels, internal pressure has the largest magnitude. In low pressure vessels, wall thickness is designed to resist vacuum. [8]
Head thickness
Alternate equations govern the appropriate head thickness:
Hemispherical:
Ellipsoidal:
Torispherical:
Rc is the crown radius. [9]
Corrosion Allowance
A margin of wall thickness must be added to account for corrosion of the vessel over time. This margin is usually between 1/16” and 3/16”.
In heat exchangers where wall thickness can affect heat transfer, smaller margins are used. [10]
Materials of Construction
The materials used in pressure vessels must maintain their strength under design conditions, withstand variation due to changing process conditions, and must resist corrosion. Commonly used materials include carbon steel, stainless steel, and various nickel alloys. [11]
References: Template:Reflist
- ^ Sinnott, R. K., and Gavin P. Towler. Chemical Engineering Design / Ray Sinnott, Gavin Towler. 2013
- ^ Sinnott, R. K., and Gavin P. Towler. Chemical Engineering Design / Ray Sinnott, Gavin Towler. 2013
- ^ Sinnott, R. K., and Gavin P. Towler. Chemical Engineering Design / Ray Sinnott, Gavin Towler. 2013
- ^ Sinnott, R. K., and Gavin P. Towler. Chemical Engineering Design / Ray Sinnott, Gavin Towler. 2013
- ^ Template:Pressure Vessel Heads. Inspection-for-Industry. http://www.inspection-for-industry.com/pressure-vessel-heads.html
- ^ Sinnott, R. K., and Gavin P. Towler. Chemical Engineering Design / Ray Sinnott, Gavin Towler. 2013
- ^ Sinnott, R. K., and Gavin P. Towler. Chemical Engineering Design / Ray Sinnott, Gavin Towler. 2013
- ^ Sinnott, R. K., and Gavin P. Towler. Chemical Engineering Design / Ray Sinnott, Gavin Towler. 2013
- ^ Sinnott, R. K., and Gavin P. Towler. Chemical Engineering Design / Ray Sinnott, Gavin Towler. 2013
- ^ Sinnott, R. K., and Gavin P. Towler. Chemical Engineering Design / Ray Sinnott, Gavin Towler. 2013
- ^ Sinnott, R. K., and Gavin P. Towler. Chemical Engineering Design / Ray Sinnott, Gavin Towler. 2013